在液化天然氣、空分裝置、氫能儲運(yùn)等工況領(lǐng)域,傳統(tǒng)管殼式換熱器因體積龐大、耐壓能力有限而難以滿足需求,而繞管式換熱器憑借其的螺旋纏繞管束結(jié)構(gòu)與高壓適應(yīng)性,成為深冷、高壓、大溫差場景的核心傳熱設(shè)備。作為緊湊型換熱器的代表,繞管式換熱器通過多層螺旋管束與殼程流體的高效逆流傳熱,在相同換熱量下體積較傳統(tǒng)管殼式減少40%~60%,同時(shí)可承受15~30MPa的超高壓環(huán)境,是能源與化工領(lǐng)域?qū)崿F(xiàn)設(shè)備小型化、高能效化的關(guān)鍵技術(shù)突破。
??一、定義與核心特征??
??1.1基本定義??
繞管式換熱器是一種由多層螺旋纏繞的細(xì)管束構(gòu)成管程、殼程流體沿軸向流動的高效換熱設(shè)備。其核心設(shè)計(jì)理念是通過螺旋纏繞增加單位體積內(nèi)的傳熱面積,并利用管束自緊效應(yīng)提升承壓能力。
1.2技術(shù)優(yōu)勢??
??高壓耐受性??:螺旋纏繞產(chǎn)生的預(yù)應(yīng)力可抵消管內(nèi)外壓差,最高承壓達(dá)30MPa。
??深冷適應(yīng)性??:管束采用低溫鋼或鋁合金,-196℃下仍保持韌性。
??自清潔能力??:螺旋流道抑制結(jié)垢,維護(hù)周期延長2~3倍。
??熱補(bǔ)償性能??:管束自由端可軸向伸縮,避免溫差應(yīng)力集中。
??二、結(jié)構(gòu)解析與傳熱機(jī)理??
??2.1典型結(jié)構(gòu)分解??
??芯筒:碳鋼或不銹鋼圓筒,作為管束纏繞基準(zhǔn),直徑200~800mm。
??螺旋管束??:多組細(xì)管按15°~30°螺旋角分層纏繞,層間填充定距條。
??殼體??:高壓厚壁筒體,與管束間形成殼程流道,內(nèi)壁可設(shè)導(dǎo)流筒。
??管箱:集流管采用多孔鍛件,實(shí)現(xiàn)管程介質(zhì)均布。
??支撐結(jié)構(gòu)??:端部管板與環(huán)形支撐圈固定管束,防止振動疲勞。
??2.2流體動力學(xué)特性??
??殼程流態(tài)??:螺旋流道誘導(dǎo)流體旋轉(zhuǎn),增強(qiáng)湍流度,傳熱系數(shù)提升20%~40%。
??管程流態(tài)??:小管徑實(shí)現(xiàn)高流速,抑制層流底層熱阻。
??2.3傳熱強(qiáng)化機(jī)制??
??逆流主導(dǎo)??:管程與殼程逆向流動,對數(shù)平均溫差大化。
??二次流效應(yīng)??:螺旋曲率誘發(fā)Dean渦流,強(qiáng)化邊界層擾動。
??高密度傳熱面??:通過多層纏繞與密排管束,單位體積傳熱面積達(dá)管殼式3倍以上。
三、制造工藝與質(zhì)量控制??
??3.1核心制造流程??
??管束預(yù)成型??:
細(xì)管經(jīng)矯直、酸洗后,在芯筒上螺旋纏繞,層間鋪設(shè)銅制定距條。
纏繞張力控制,確保管束層間緊密貼合。
??管束固定??:
端部采用環(huán)形鍛件+電子束焊接,形成整體管束模塊。
液壓脹管使管束與芯筒貼合。
??殼體組裝??:
厚壁筒體卷制+縱縫焊接,內(nèi)壁堆焊耐蝕層。
管束整體吊裝入殼,兩端法蘭螺栓預(yù)緊。
3.2特殊工藝要求??
??深冷處理??:管束在液氮中冷卻至-196℃,釋放纏繞殘余應(yīng)力。
??氦檢漏測試??:管程充氦至設(shè)計(jì)壓力,質(zhì)譜儀檢測泄漏率<1×10??mbar·L/s。
??流阻測試??:殼程水循環(huán)測試,壓降偏差≤5%。
3.3數(shù)字化制造技術(shù)??
??纏繞數(shù)控系統(tǒng)??:6軸機(jī)器人同步控制管材送進(jìn)與芯筒旋轉(zhuǎn),定位精度±0.1mm。
??AI工藝優(yōu)化??:基于歷史數(shù)據(jù)訓(xùn)練神經(jīng)網(wǎng)絡(luò),預(yù)測理想纏繞張力與速度組合。
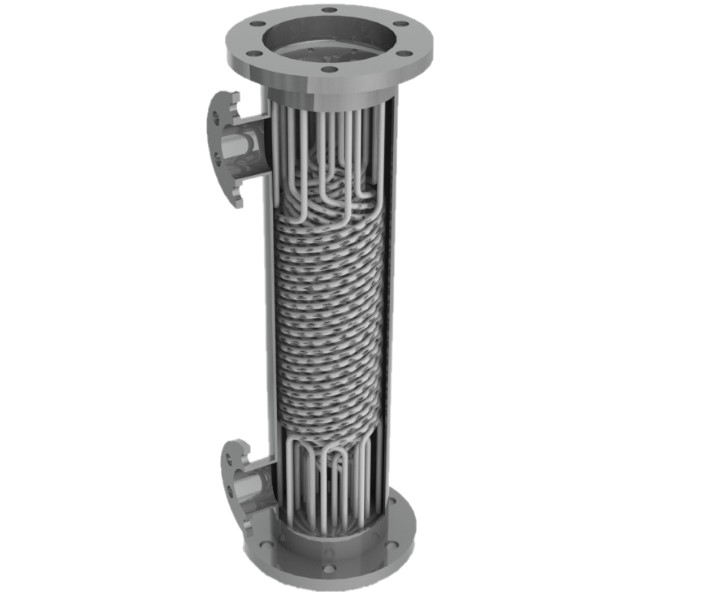